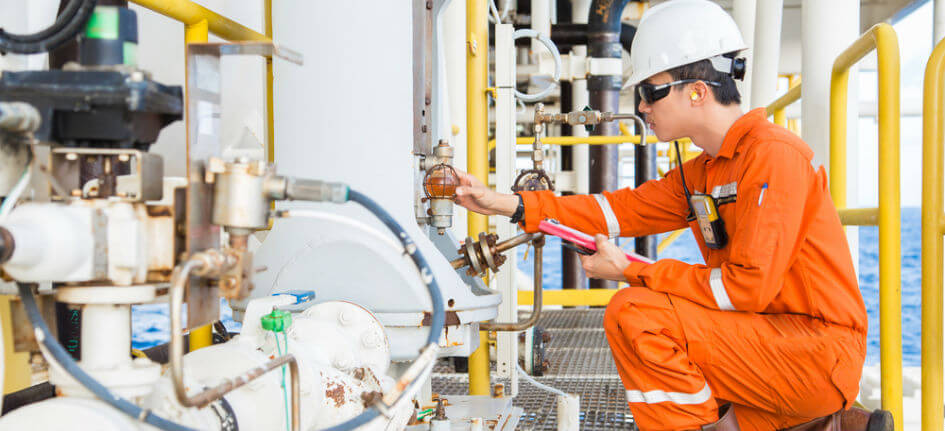
Code | Date | Venue | Fees | Register |
---|---|---|---|---|
ME110-01 | 11-05-2025 | Dubai | USD 5450 | |
ME110-02 | 16-06-2025 | Kuala-Lumpur | USD 5950 | |
ME110-03 | 17-08-2025 | Amman | USD 5450 | |
ME110-04 | 21-12-2025 | Dubai | USD 5450 |
This seminar will enable delegates to remain abreast of the latest researched trends, techniques and strategies to improve the condition and performance of their operational process. This hands-on int ...
It is estimated that electrical drives and other rotating equipment consume about 50% of the total electrical energy consumed in the world today. The cost of maintaining electrical motors can be a sig ...
A sudden loss of power will disrupt most business operations and could lead to a company being unable to trade. Where a company regards electrical power as critical then there will be a need for a con ...
An Uninterruptible Power Supply (UPS) is a device that sits between a power supply (e.g. a wall outlet) and a device (e.g. a computer) to prevent undesired features of the power source (outages, sags, ...
This course for industry aims to convey the latest thinking and best practice of machinery vibration monitoring and analysis via lectures, case studies, video films and program activities. The course ...
The purpose of this course is to provide advance training in gas chromatography techniques and demonstrate their application to practical industry and laboratory problems. The course covers: major com ...
Gas turbines became widely adopted and many thousands of sets are now installed worldwide. The development of gas turbine from the theoretical stage to its present worldwide adoption has three maim in ...
This course is designed to increase the trouble shooting skills and fault diagnostic processesfor technicians and maintenance teams on LV equipment. The practical elements of thecourse centre on advan ...
As refiners and chemical producers worldwide see higher crude oil and feed prices and continued demand for clean transportation fuels and lower production costs, a sound knowledge of clean fuel techno ...
Power plant and other petrochemical industries do deal with different types of valves. All piping systems are fitted with valves for controlling purposes or safety requirements. Understanding the func ...
This course is designed to integrate the various aspects and techniques within the field of separation science. We will cover theory, instrumentation, and practice of modern separation techniques incl ...
Ammonia is one of the most important inorganic basic chemicals, not only for the manufacture of fertilizers (85%) but also for the production of plastics, fibers, explosives, and intermediates for dye ...
This BTS training course is designed for personnel working in the petroleum depot operations seeking to acquire more knowledge on effective handling of depot operations, storage, design standards, dep ...
One of the most important separations, qualitative and quantitative technic is chromatograph, It is need time to gain experience in this field of analysis so, training is very effective to help traine ...
Centrifugal Compressors a play a very essential role in many petrochemical and industrial plants. Centrifugal compressors in general runs at very high speeds, exposed to high temperature. The compress ...
The duty of a circuit breaker is to switch on and switch off, once or repeatedly several times different electrical circuits during normal as well as abnormal operating conditions. Circuit breakers an ...
The duty of a circuit breaker is to switch on and switch off, once or repeatedly several times different electrical circuits during normal as well as abnormal operating conditions. Circuit breakers an ...
The main aim of the programme is to introduce participants to up-to-date developments, knowledge and practice in thermal desalination technologies, with emphasis on process design characteristics and ...
This course covers the theoretical and practical operation of common electrical equipment and components, as well as provides participants with the necessary knowledge and skills to perform electrical ...
Successful completion of this three-day, instructor-led course will enhance the participant’s understanding of how to troubleshoot the full line of Palo Alto Networks® next-generation firewalls. Part ...
Learn about the new enhanced capabilities of the Windows 2019 starting from server virtualization, storage, software-defined networking, server management and automation, web and application platform, ...
This five full-day course is designed to provide your valuable attendees with a comprehensive knowledge about Gas Lift design, operation, optimization, and troubleshooting in the oilfield. The course ...
Gas turbine engines are generally classified based on the type and nature of application, size and location. This chapter contains a general overview of the different types of gas turbines in use, and ...
This 5 days seminar is designed to provide excellent understanding on both a theoretical and practical level for power generators. The workshop starts at a basic level, to ease the engineer and techni ...
This program is designed for engineers and technicians from a wide range of abilities and backgrounds and will provide an excellent introduction to the fundamentals of Heating, Ventilation and Air-con ...
The equipment needs to be operated in a safe manner securing continuity of supply. This requires the equipment to be designed, installed, commissioned, operated, and maintained in a satisfactory manne ...
In this 5 day accelerated course, you will learn to install, configure, and maintain Unified Computing System (UCS) B-Series and C-Series servers with a strong emphasis on Cisco UCS B-Series Blade Ser ...
Implementing and Troubleshooting the Cisco Cloud Infrastructure (CLDINF) v1.0 is a newly created five day instructor-led training designed to prepare you with the knowledge and hands-on experience to ...
The growth of modern technology has confronted the analytical chemist with a host of new and increasingly complex materials, and has posed more stringent demands for greater sensitivity, reliability, ...
The purpose of this course is to provide advanced training in liquid chromatography techniques and demonstrate their application in practical industry and laboratory problems. The course covers: major ...
This course provides the appropriate mix of fundamentals, methodologies, best industry practices, and practical tools to enhance the competencies and improve the performance of operation and maintenan ...
The course covers all topics relating to both AC motors and their drives. AC motors represent industry's workhorse in all applications. It is no exaggeration to suggest that more than half of the ener ...
Put best practices, computer technology, and team power to work for your company! Computerized tank inventory, shipment, and receipts management, and crude and product blending are key to a profitable ...
This course describes the principles of engines and generators starting with the fundamentals, discusses the options available and the constructional details of engines, the electrical alternators and ...
This course will provide the candidates with extensive knowledge including tips, tricks and tools covering the fundamentals of power transformers and their testing. It will greatly assist you in commu ...
Advanced Firewall Troubleshooting is the next-level follow-on course to Palo Alto Networks® Essentials 1: Installation, Configuration, and Management (PAN-EDU-201) and Essentials 2: Extended Firewall ...
Industrial processes today operate on very large scales with the advent of modern industrial plants. Such plants sometimes operate hundreds of equipment, not to mention thousands of instruments for th ...
Whatever your hydraulic applications, you can increase your knowledge of the fundamentals, improve your maintenance programs and become an excellent trouble-shooter of problems in this area by attendi ...
This comprehensive course is designed to provide an in-depth perspective of pump technology in terms of selection, operation, maintenance and repair. Topics covered include pump types and terminology, ...
This comprehensive course is designed to provide an in-depth perspective of pump technology in terms of selection, operation, maintenance and repair. Topics covered include pump types and terminology, ...
Power Plant and other petrochemical industries do deal with different types of valves. All piping systems are fitted with valves for controlling purposes or safety requirements. Understanding the func ...
There is an alarming trend in industry to discount the potential contribution of the Technical/Operations function to productivity improvement, product quality and gains in market share. Principles ta ...
The reactors play a capital role in many factory process operations. Basically a reaction is an apparatus or structure in which fissile material can be made to undergo a controlled, self-sustaining nu ...
Excellent Troubleshooting skills are considered a core competency for 'Best-in-Class' industrial companies. If your company’s goals include minimizing downtime then
This course is to provide the trainees with a strong background in the field of Advanced Rotating Equipment (Pumps, Compressors, and turbines) maintenance and troubleshooting. In addition, the traine ...
Pumps and compressors are the tow pieces of equipment which are used in almost all manufacturing and processing plants. The effectiveness of their selection, specifications, operations, maintenance an ...
Rotating Equipment's are the pieces of equipment which are used in almost all manufacturing and processing plants. The effectiveness of their selection, specifications, operations, maintenance and tro ...
Within the boiler, piping and pressure vessel industry, control and safety relief are of Most essential importance. Pressure relief valves are the last line of defense against Catastrophic failure or ...
This Course Has Been Designed for Individuals Who is Familiar with Steam Turbine to Understand and be able to make decisions relating for Steam Turbine Failure Analysis Inspection and Troubleshooting ...
There is considerable interest among people who operate and maintain electrical power systems in a Wide range of topics relating to equipment maintenance and testing. This is because condition and rel ...
The Symantec Data Center Server Advanced 6.7 Diagnostics and Troubleshooting course is designed for the IT security management professional tasked with troubleshooting Data Center Security Server Adva ...
The effective management and operation of an oil and gas terminal is essential for a successful business. The processing, transporting and storing of crude oil and refined petroleum products, in tank ...
Power Transformers are essential devices in electricity supply. Their ratings can vary from small size distribution transformers up to very large power transformers of 1000 MVA or more. In terms of vo ...
This 5-day workshop is designed to provide excellent understanding on both a theoretical and practical level to attendees. The workshop starts at a basic level, to ease the engineer and technician int ...
The Troubleshooting Cisco Data Center Infrastructure (DCIT) v7.0 course shows you how to troubleshoot LAN, SAN, Cisco Data Center Unified Fabric, Cisco Unified Computing System (UCS), and Cisco Applic ...
CTCOLLAB v1.0 is a comprehensive course that enables the learner to troubleshoot Cisco Unified Communications Manager, Cisco VCS-C, and Cisco Expressway series in a multisite voice and video network. ...
Accurate troubleshooting and subsequent repair of electrical equipment is necessary in today’s sophisticated industrial environments to ensure continued efficient operation and productivity of the equ ...
This course will cover how to establish and apply a general troubleshooting methodology as well as how to conduct process/equipment specific troubleshooting. Definitions of good/normal performance wil ...
This seminar will enable delegates to remain abreast of the latest researched trends, techniques and strategies to improve the condition and performance of their operational process. This hands-on int ...
It is estimated that electrical drives and other rotating equipment consume about 50% of the total electrical energy consumed in the world today. The cost of maintaining electrical motors can be a sig ...
A sudden loss of power will disrupt most business operations and could lead to a company being unable to trade. Where a company regards electrical power as critical then there will be a need for a con ...
An Uninterruptible Power Supply (UPS) is a device that sits between a power supply (e.g. a wall outlet) and a device (e.g. a computer) to prevent undesired features of the power source (outages, sags, ...
This course for industry aims to convey the latest thinking and best practice of machinery vibration monitoring and analysis via lectures, case studies, video films and program activities. The course ...
The purpose of this course is to provide advance training in gas chromatography techniques and demonstrate their application to practical industry and laboratory problems. The course covers: major com ...
Gas turbines became widely adopted and many thousands of sets are now installed worldwide. The development of gas turbine from the theoretical stage to its present worldwide adoption has three maim in ...
This course is designed to increase the trouble shooting skills and fault diagnostic processesfor technicians and maintenance teams on LV equipment. The practical elements of thecourse centre on advan ...
Providing services with a high quality that are satisfying the requirements
Appling the specifications and legalizations to ensure the quality of service.
Best utilization of resources for continually improving the business activities.
BTS keen to selects highly technical instructors based on professional field experience
Since BTS was established, it considered a training partner for world class oil & gas institution
1st floor, Incubator Buildingو Masdar City, Abu Dhabi, UAE
Sun to Fri 09:00 AM to 06:00 PM
Contact Us anytime!
Request Info