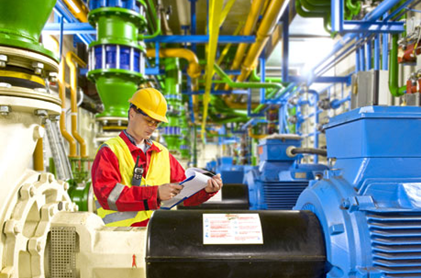
Code | Date | Venue | Fees | Register |
---|---|---|---|---|
ME164-02 | 15-06-2025 | Casablanca | USD 5950 | |
ME164-03 | 08-09-2025 | Istanbul | USD 5950 | |
ME164-04 | 23-11-2025 | Dubai | USD 5450 |
Upon completion of this course, participants will gain a basic understanding of the main components and subsystems of audit procedures. They will learn to critique the advantages, applications, perfor ...
This course provides attendees the training needed to extend their knowledge of machinery diagnostic techniques and rotor dynamics as applied to rotating machinery. In particular, they will learn the ...
This course builds upon the Data Acquisition computer based training, providing the foundation for machinery diagnostics. The hands-on approach gives students the experience they need to feel confiden ...
This course is for experienced mechanical equipment engineers to develop and expand their capabilities in monitoring and problem analysis of turbo machinery.
In this 5-day course, participants will gain a strong technical and practical understanding of bearing design features and implications of many bearings types. This course will provide the participant ...
Upon completion of this course, participants will gain a basic understanding of the main components and subsystems of audit procedures. They will learn to critique the advantages, applications, perfor ...
This course provides attendees the training needed to extend their knowledge of machinery diagnostic techniques and rotor dynamics as applied to rotating machinery. In particular, they will learn the ...
This course builds upon the Data Acquisition computer based training, providing the foundation for machinery diagnostics. The hands-on approach gives students the experience they need to feel confiden ...
This course is for experienced mechanical equipment engineers to develop and expand their capabilities in monitoring and problem analysis of turbo machinery.
In this 5-day course, participants will gain a strong technical and practical understanding of bearing design features and implications of many bearings types. This course will provide the participant ...
Upon completion of this course, participants will gain a basic understanding of the main components and subsystems of audit procedures. They will learn to critique the advantages, applications, perfor ...
This course provides attendees the training needed to extend their knowledge of machinery diagnostic techniques and rotor dynamics as applied to rotating machinery. In particular, they will learn the ...
This course builds upon the Data Acquisition computer based training, providing the foundation for machinery diagnostics. The hands-on approach gives students the experience they need to feel confiden ...
Providing services with a high quality that are satisfying the requirements
Appling the specifications and legalizations to ensure the quality of service.
Best utilization of resources for continually improving the business activities.
BTS keen to selects highly technical instructors based on professional field experience
Since BTS was established, it considered a training partner for world class oil & gas institution
1st floor, Incubator Buildingو Masdar City, Abu Dhabi, UAE
Sun to Fri 09:00 AM to 06:00 PM
Contact Us anytime!
Request Info