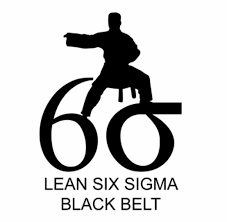
This course is complying with the requirements of the International Association for Six-Sigma Certification.
Tools Used
Excel 2013 and Minitab 16
Book Reference
Introduction to Materials Management - 6th edition - 2008 - J. R. Tony Arnold, Stephen N. Chapman and Lloyd M. Clive - Prentice Hall
How to Implement Lean Manufacturing - 2010 - Lonnie Wilson - McGraw-Hill
Implementing Six Sigma - 2nd Edition - 2003 - Forrest W. Breyfogle Iii - John Wiley & Sons
Learning To See - Version 1.2 - 1999 - Mike Rother And John Shook - Lean Enterprise Institute
Six Sigma Quality Improvement with Minitab - 2nd edition - 2011 - G. Robin Henderson - John Wiley & Sons
Benefits of Attendees:
By the end of this course delegates will be able to:
This interactive Training will be highly interactive, with opportunities to advance your opinions and ideas and will include;
DEFINE: Project Definition
DEFINE: Change Management Teams
MEASURE: Tools and Objectives
MEASURE: Establishing Process Baseline
MEASURE: Process Capability
ANAL YZE: Introduction to Linear Regression Analysis
ANALYZE: Lean Thinking
IMPROVE: Tools and Objectives
CONTROL: Tools and Objectives
BTS attendance certificate will be issued to all attendees completing minimum of 75% of the total course duration.
Code | Date | Venue | Fees | Register |
---|---|---|---|---|
QUA103-05 | 26-01-2025 | Jeddah | USD 5450 | |
QUA103-01 | 11-05-2025 | Dubai | USD 5450 | |
QUA103-02 | 13-07-2025 | Marrakesh | USD 5950 | |
QUA103-03 | 21-09-2025 | Dubai | USD 5450 | |
QUA103-04 | 14-12-2025 | Cairo | USD 5450 |
Six Sigma is a quality philosophy, a process for improvement, a quality metric, and can be used to establish and reach aggressive goals, which are integrated with your company business and operating c ...
This course uses renowned Motorola methodology to identify and solve problems in organizations. Targeting the yellow belt level, this course will provide participants with the knowledge to identify im ...
Certified Six Sigma Project Managers Earn Much More Than Their Counterparts. Six Sigma Green Belt Course leading to Six Sigma Green Belt Certification offers a unique opportunity to get yourself certi ...
The Six Sigma methodology is a systematic application focused on achieving significant financial results and increasing customer satisfaction. When properly deployed on carefully selected business pro ...
Providing services with a high quality that are satisfying the requirements
Appling the specifications and legalizations to ensure the quality of service.
Best utilization of resources for continually improving the business activities.
BTS keen to selects highly technical instructors based on professional field experience
Since BTS was established, it considered a training partner for world class oil & gas institution
1st floor, Incubator Buildingو Masdar City, Abu Dhabi, UAE
Sun to Fri 09:00 AM to 06:00 PM
Contact Us anytime!
Request Info