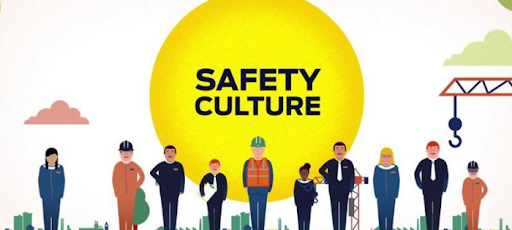
Participants will explore how to foster commitment to safety at all organizational levels, from senior management to frontline employees, ensuring that safety becomes an integral part of daily operations. The course focuses on proactive approaches, continuous improvement, and behavioral change techniques to develop and sustain a positive safety environment.
After this course, the participants will be able to:
This interactive Training will be highly interactive, with opportunities to advance your opinions and ideas and will include;
1.1 What is Safety Culture?
1.2 Key Components of Safety Culture
1.3 The Safety Culture Maturity Model
1.4 Case Studies: Safety Culture Success Stories
2.1 The Role of Leadership in Safety Culture
2.2 Engaging Employees in Safety Initiatives
2.3 Safety Communication
3.1 Understanding Behavioral Safety
3.2 Changing Unsafe Behaviors
3.3 Change Management for Safety Culture
4.1 Proactive vs. Reactive Safety Approaches
4.2 Hazard Identification and Risk Assessment
4.3 Developing Safety Procedures and Protocols
5.1 Safety Performance Metrics and KPIs
5.2 Safety Audits and Inspections
5.3 Continuous Improvement in Safety Culture
5.4 Final Group Exercise
Developing an Action Plan: Participants will work in groups to develop a tailored action plan for improving safety culture in their respective organizations. The plan will focus on the elements covered in the course, ensuring practical takeaways.
BTS attendance certificate will be issued to all attendees completing minimum of 80% of the total course duration.
Code | Date | Venue | Fees | Register |
---|---|---|---|---|
HSE221-01 | 13-04-2025 | Amman | USD 5450 | |
HSE221-02 | 06-07-2025 | Cairo | USD 5450 | |
HSE221-03 | 05-10-2025 | Dubai | USD 5450 | |
HSE221-04 | 14-12-2025 | Dubai | USD 5450 |
This five-day course addresses the key components of and the tools required for preparing, implementing and managing an effective Occupational Health and Safety Program as required by the Occupational ...
Striving for safety excellence has to be every safety professional’s endeavor and aspiration. This “must attend” Advanced Safety Leadership course will provide you with powerful tools that with effort ...
This program offers the cost-effective solutions you need to keep your people safe-and to keep OSHA inspectors off your doorstep! You'll get a comprehensive update on the very latest in OSHA's ever-ch ...
Providing services with a high quality that are satisfying the requirements
Appling the specifications and legalizations to ensure the quality of service.
Best utilization of resources for continually improving the business activities.
BTS keen to selects highly technical instructors based on professional field experience
Since BTS was established, it considered a training partner for world class oil & gas institution
1st floor, Incubator Buildingو Masdar City, Abu Dhabi, UAE
Sun to Fri 09:00 AM to 06:00 PM
Contact Us anytime!
Request Info