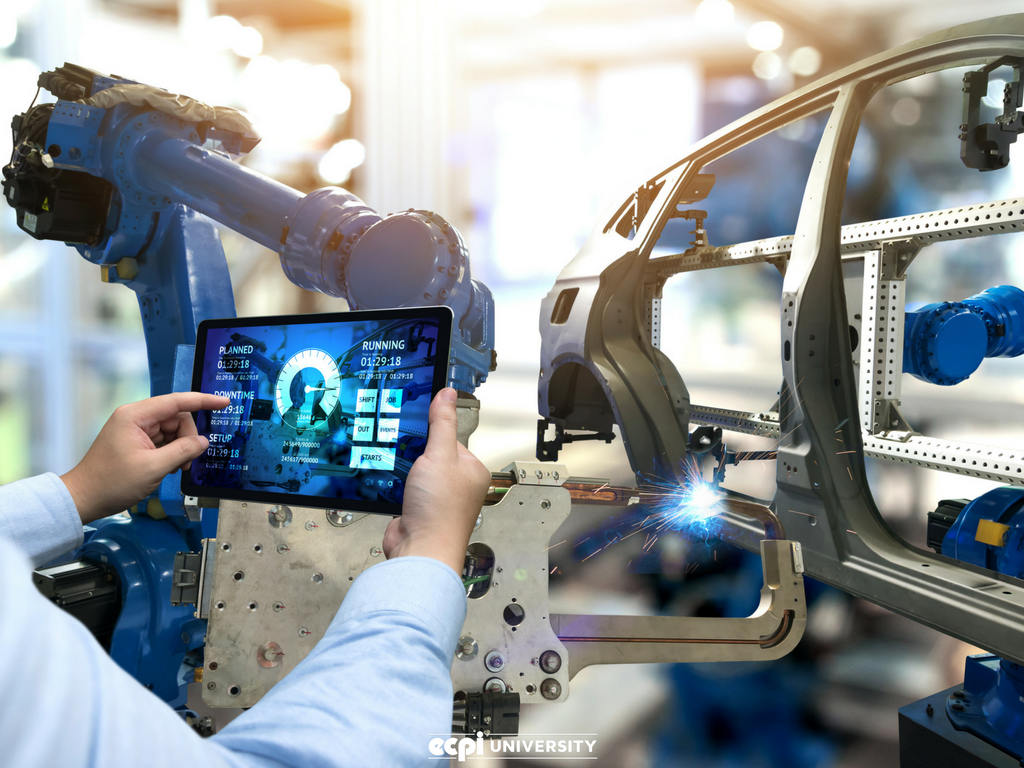
Code | Date | Venue | Fees | Register |
---|---|---|---|---|
MI101-02 | 22-06-2025 | Amman | USD 5450 | |
MI101-03 | 21-09-2025 | Dubai | USD 5450 | |
MI101-04 | 15-12-2025 | Istanbul | USD 5950 |
While developing the individual’s leadership skills specifically in the area of Strategic planning, development and execution of plans, organizational goals will be achieved more efficiently. The cour ...
At the end of this course the attendees will gain the knowledge about maintenance, computerized maintenance programs & maintenance planning basic concepts including maintenance background overview and ...
Providing services with a high quality that are satisfying the requirements
Appling the specifications and legalizations to ensure the quality of service.
Best utilization of resources for continually improving the business activities.
BTS keen to selects highly technical instructors based on professional field experience
Since BTS was established, it considered a training partner for world class oil & gas institution
1st floor, Incubator Buildingو Masdar City, Abu Dhabi, UAE
Sun to Fri 09:00 AM to 06:00 PM
Contact Us anytime!
Request Info