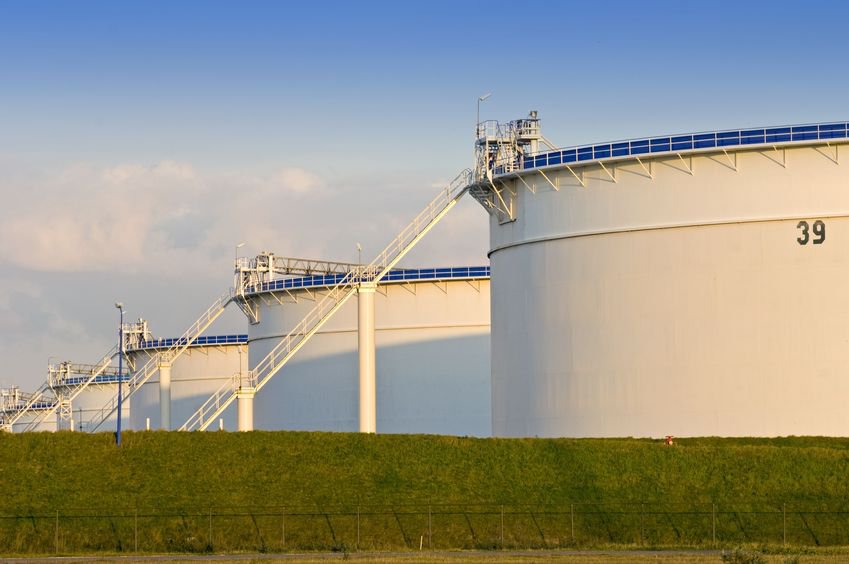
Code | Date | Venue | Fees | Register |
---|---|---|---|---|
MI264-02 | 25-05-2025 | Dubai | USD 5450 | |
MI264-03 | 21-09-2025 | Cairo | USD 5450 |
Providing services with a high quality that are satisfying the requirements
Appling the specifications and legalizations to ensure the quality of service.
Best utilization of resources for continually improving the business activities.
BTS keen to selects highly technical instructors based on professional field experience
Since BTS was established, it considered a training partner for world class oil & gas institution
1st floor, Incubator Buildingو Masdar City, Abu Dhabi, UAE
Sun to Fri 09:00 AM to 06:00 PM
Contact Us anytime!
Request Info