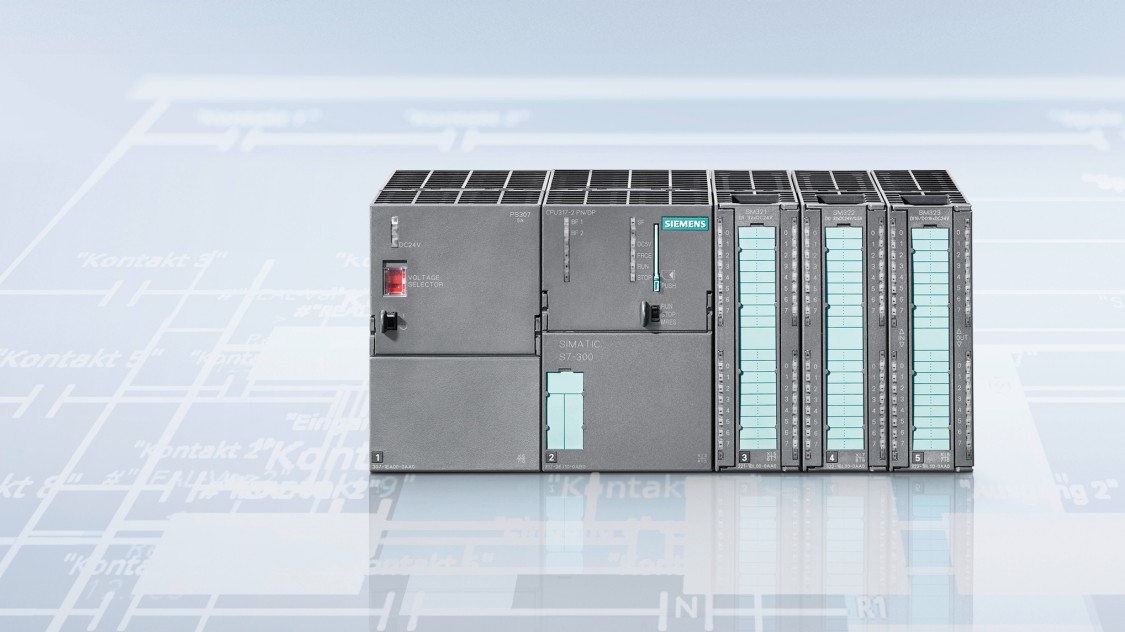
While this course is ideal for engineers who are new to PLCs, much of the contents and additional material in the extensive manual will be of value to those who already have the basic skills, but need a wider perspective for larger and more challenging tasks ahead.
The information contained in this course advances from the basics to challenge even the most experienced engineer in the industry today.
The course is supported by Video demonstrating PLC Programming techniques.
This course aims to enable the participants to:
This course is designed for:
Day 1
Chapter 1: INTRODUCTION TO PROGRAMMABLE CONTROLLERS
Number Systems and Codes
Chapter 2: PLC COMPONENTS AND SYSTEMS
Processors, the Power Supply, and Programming Devices
The Memory System and I/O Interaction
The Input / Output System
Day 2
Chapter 3: PLC PROGRAMMING
Programming Languages
The IEC 1131 Standard and Programming Language
Day 3
System Programming and Implementation
PLC System Documentation
Case Studies “Siemens S7 & Allen Bradley”
Day 4
Chapter 4: PLC COMMUNICATION & NETWORKS
Local Area Networks
I/O Bus Networks
Case Studies “Siemens S7 & Allen Bradley”
Chapter 5: PLC Installation, Start-up, Troubleshooting and Maintenance
PLC Start-Up and Maintenance
System Selection Guidelines
Case Studies “Siemens S7 & Allen Bradley”
Day 5
Chapter 6: PLC Programming Application Exercises
Case Studies “Siemens S7 & Allen Bradley”
Code | Date | Venue | Fees | Register |
---|---|---|---|---|
IE138-01 | 15-06-2025 | Dubai | USD 5450 | |
IE138-02 | 10-08-2025 | Muscat | USD 5450 | |
IE138-03 | 12-10-2025 | Marrakesh | USD 5950 | |
IE138-04 | 21-12-2025 | Dubai | USD 5450 |
Providing services with a high quality that are satisfying the requirements
Appling the specifications and legalizations to ensure the quality of service.
Best utilization of resources for continually improving the business activities.
BTS keen to selects highly technical instructors based on professional field experience
Since BTS was established, it considered a training partner for world class oil & gas institution
1st floor, Incubator Buildingو Masdar City, Abu Dhabi, UAE
Sun to Fri 09:00 AM to 06:00 PM
Contact Us anytime!
Request Info