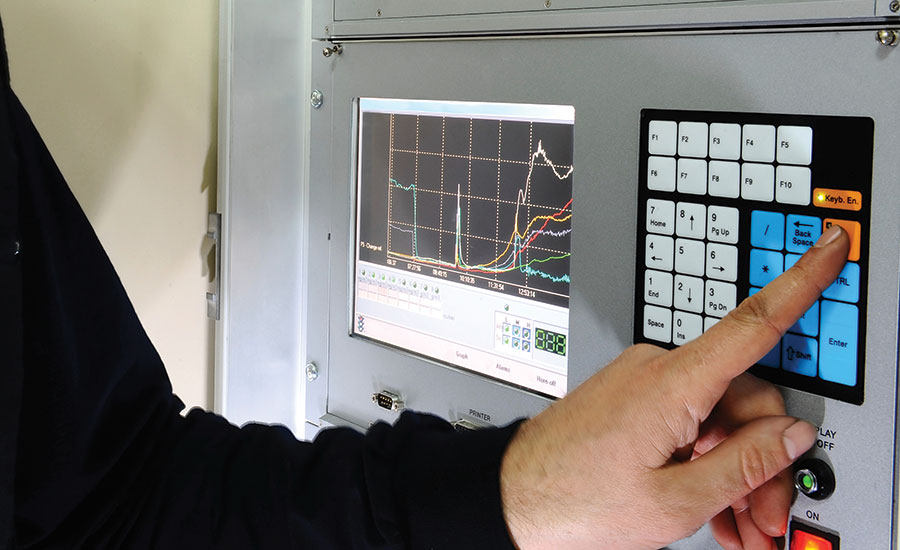
Code | Date | Venue | Fees | Register |
---|---|---|---|---|
IE136-01 | 20-04-2025 | Dubai | USD 5450 | |
IE136-02 | 22-06-2025 | Casablanca | USD 5950 | |
IE136-03 | 26-10-2025 | Amman | USD 5450 | |
IE136-04 | 30-11-2025 | Dubai | USD 5450 |
This programme takes an in-depth look at closed loop control. Although the subject of many hundreds of articles, books, and courses, the basic elements of automatic process control are still widely m ...
Providing services with a high quality that are satisfying the requirements
Appling the specifications and legalizations to ensure the quality of service.
Best utilization of resources for continually improving the business activities.
BTS keen to selects highly technical instructors based on professional field experience
Since BTS was established, it considered a training partner for world class oil & gas institution
1st floor, Incubator Buildingو Masdar City, Abu Dhabi, UAE
Sun to Fri 09:00 AM to 06:00 PM
Contact Us anytime!
Request Info