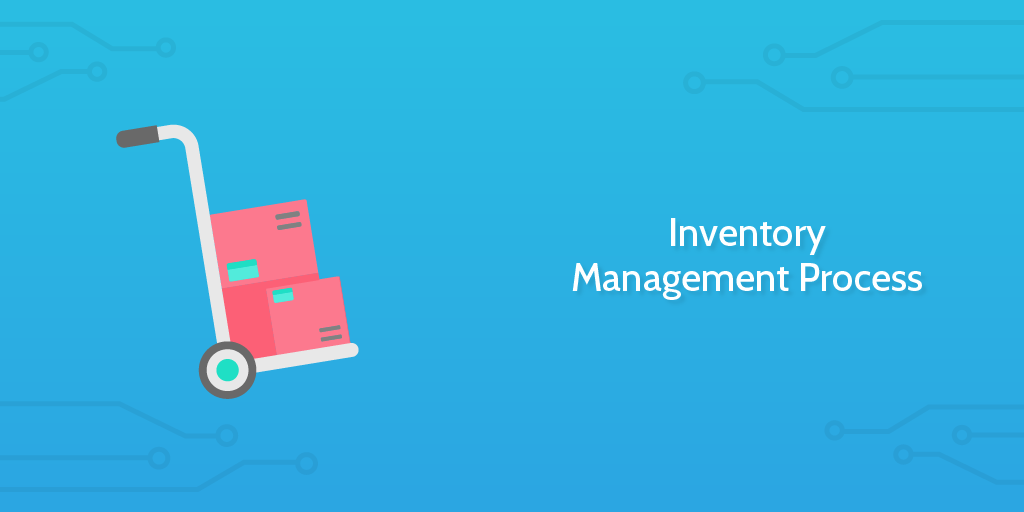
Personal impact:
Organizational impact:
Competencies:
Day 1- Supply Chain
The Supply chain definitions, history and key aspects
Relationships and materials flows in the chain
Day 2-Products & Stock
Product classification
Inventory costs and service
Day 3- Replenishment Methods
How much stock should be held?
Replenishment methods for independent demand
Other replenishment methods
Day 4 – Forecasting and Stock Control
Demand Forecasting
Stock Coding
The method by which stock is coded is important in the overall management process, this session will examine:
Stock Recording
This session looks at stock recording, critical aspect of stock control and if done incorrectly is the source of many subsequent errors
Stock Checking
Much time can be spent on this activity, but there are methods to both minimize the time and at the same time increase checking accuracy. This session examines such aspects
Day 5- Improvements
Model for planning inventory
BTS attendance certificate will be issued to all attendees completing minimum of 80% of the total course duration.
Code | Date | Venue | Fees | Register |
---|---|---|---|---|
PRO117-05 | 23-12-2024 | Istanbul | USD 5950 | |
PRO117-01 | 27-04-2025 | Dammam | USD 5450 | |
PRO117-02 | 13-07-2025 | Dubai | USD 5450 | |
PRO117-03 | 21-09-2025 | Dubai | USD 5450 | |
PRO117-04 | 16-11-2025 | Casablanca | USD 5950 |
Effective upstream Supply Chain Management is increasingly about doing the “right things” and then doing “things right” within the Supply Chain in order to improve and sustain overall business perform ...
World-class organizations view best practices in purchasing and inventory management as essential skill sets needed by all employees involved in the procurement process.
Knowledge of Inventory Management is critical for the effective management of procurement and the supply chain, however Inventory it is commonly not understood. Therefore too high levels of inventory ...
Knowledge of Inventory Management is critical for the effective management of procurement and the supply chain, however Inventory it is commonly not understood. Therefore too high levels of inventory ...
Providing services with a high quality that are satisfying the requirements
Appling the specifications and legalizations to ensure the quality of service.
Best utilization of resources for continually improving the business activities.
BTS keen to selects highly technical instructors based on professional field experience
Since BTS was established, it considered a training partner for world class oil & gas institution
1st floor, Incubator Buildingو Masdar City, Abu Dhabi, UAE
Sun to Fri 09:00 AM to 06:00 PM
Contact Us anytime!
Request Info