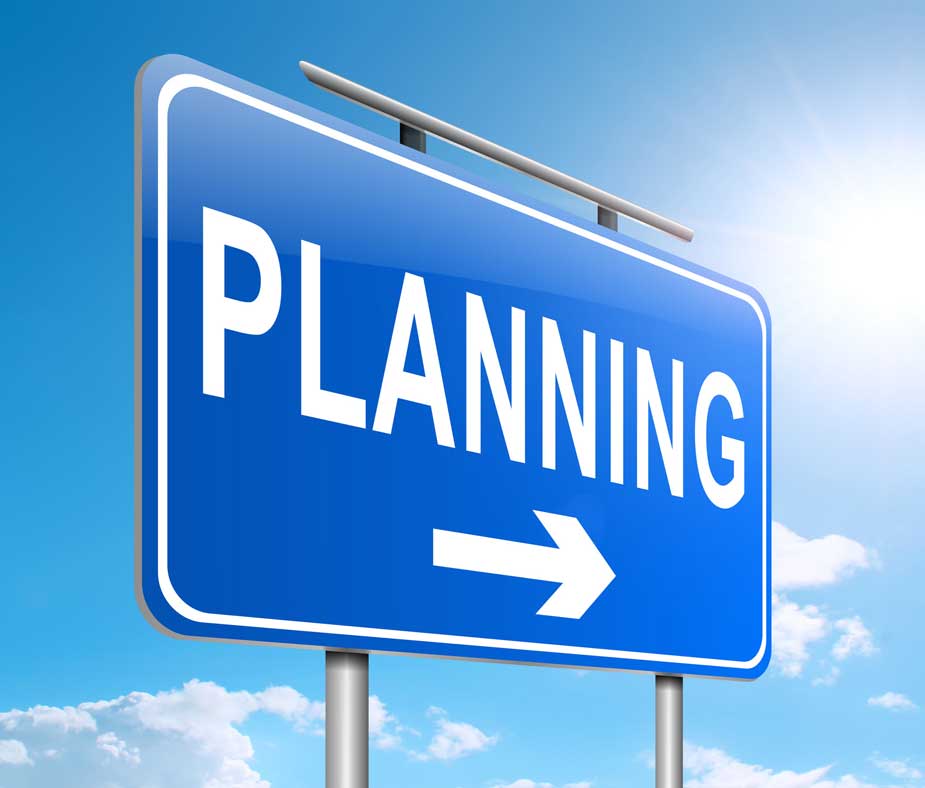
After completing these workshop learners will better understand:
Delegates should represent a wide range of personnel in the organization who are involved in, or dependent on, effective maintenance planning, scheduling and work control.
These should include:
This interactive Training will be highly interactive, with opportunities to advance your opinions and ideas and will include;
Module One
Module Two
Module Three
Module Four
BTS attendance certificate will be issued to all attendees completing minimum of 80% of the total course duration.
Code | Date | Venue | Fees | Register |
---|---|---|---|---|
MI169-01 | 19-01-2025 | Dubai | USD 5450 | |
MI169-02 | 01-06-2025 | Dubai | USD 5450 | |
MI169-03 | 10-08-2025 | Amman | USD 5450 | |
MI169-04 | 23-11-2025 | Riyadh | USD 5450 |
This highly interactive training course enables you to develop a powerful vision for asset & maintenance management improvement and improve your abilities to successfully promote and adapt changes in ...
This course enables you to develop a powerful vision for asset & maintenance management improvement and improve your abilities to successfully promote and adapt changes in the work place. You will lea ...
This 5 day training session combines a lecture series with practical exercises to give the delegates an appreciation of the role of Audits and Inspections in a progressive Safety Management System. Ma ...
Most organizations now have implemented an HSE Management System. An essential part of any HSE-MS is to provide some means of measuring performance and to provide feedback for management review. The H ...
Every system however good on paper, needs to be checked if it actually works in practice. How much more important is this need when what is at stake is not only money but human lives? There are two le ...
Providing services with a high quality that are satisfying the requirements
Appling the specifications and legalizations to ensure the quality of service.
Best utilization of resources for continually improving the business activities.
BTS keen to selects highly technical instructors based on professional field experience
Since BTS was established, it considered a training partner for world class oil & gas institution
1st floor, Incubator Buildingو Masdar City, Abu Dhabi, UAE
Sun to Fri 09:00 AM to 06:00 PM
Contact Us anytime!
Request Info