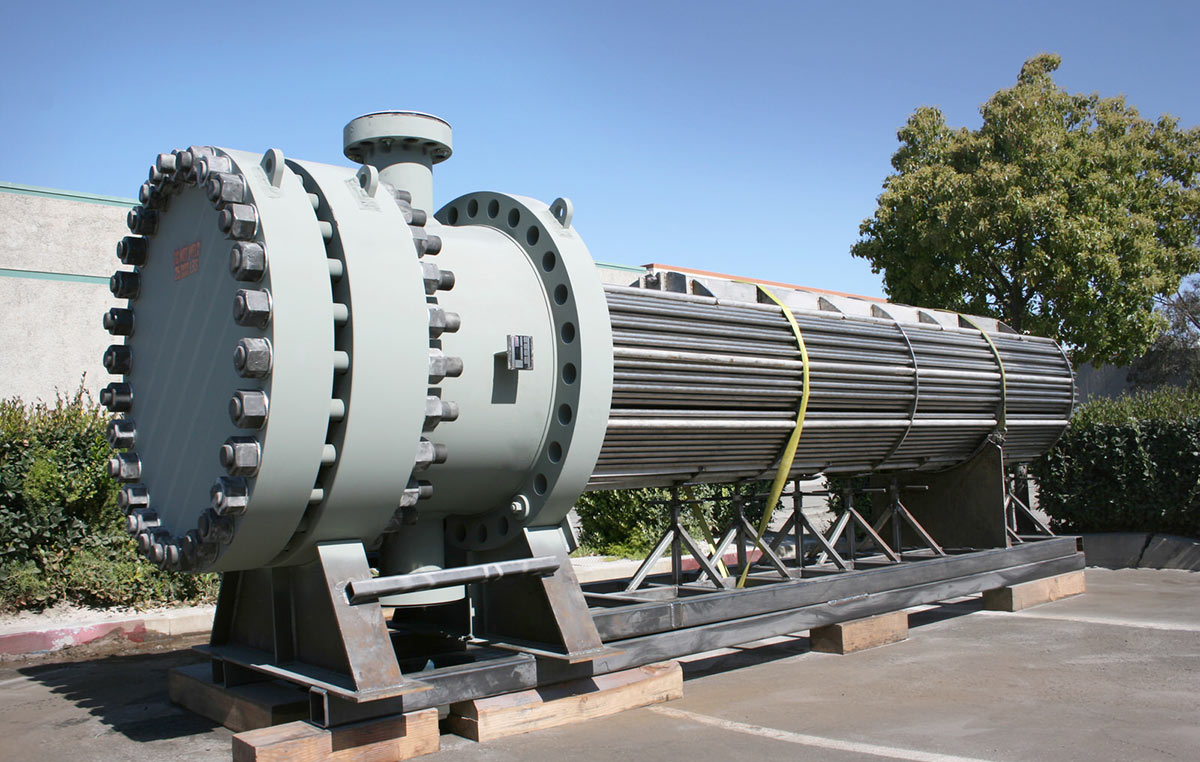
Day 1 :
Day 2 :
Day 3 :
Day 4 :
Day 5 :
BTS attendance certificate will be issued to all attendees completing minimum of 80% of the total course duration.
Code | Date | Venue | Fees | Register |
---|---|---|---|---|
ME147-01 | 04-05-2025 | Dubai | USD 5450 | |
ME147-02 | 01-06-2025 | Cairo | USD 5450 | |
ME147-03 | 14-09-2025 | Marrakesh | USD 5950 | |
ME147-04 | 21-12-2025 | Dubai | USD 5450 |
This course will provide a comprehensive review of the various aspects of engineered safety and mechanical integrity in refineries, oil & gas plants and petrochemical plants. Principal emphasis is pl ...
This course introduces the basics and fundamental concepts and applications of mechanical engineering. The course starts with an introduction to the basic principles of mechanical drawings such as tol ...
This five-day foundation level course is for engineers and technicians seeking an in-depth understanding of centrifugal, reciprocating, and screw compressors. This course provides basic knowledge of c ...
Process engineering is at the heart of much of the chemical, oil, gas, and petrochemical industries. It requires familiarity not only with chemical engineering principles, but also with many of the ot ...
Heat exchangers are important and expensive pieces of equipment that are used in a wide variety of industries. This course will enable you to improve heat exchanger effectiveness and extend the equipm ...
Mechanical engineering in simple terms deals with any equipment that moves; this is what makes it perhaps the most broad and diverse of engineering disciplines. The mechanical discipline essentially d ...
Engineers, technicians, maintainers and operators who may not have a mechanical background are often given the responsibility for the procurement, installation, operation and maintenance of mechanical ...
This course for engineers and piping system designers reviews the key areas associated with the design of piping systems for oil and gas facilities. The course is focused on four areas: codes and stan ...
This training program aims at providing the participants with a comprehensive theoretical and practical knowledge, practical aspects, and enhancing their knowledge and skills for basics of mechanical ...
In this 5-day course, participants will gain a strong technical and practical understanding of mechanical seals and gland packing through the exploration of design features and implications of many se ...
This course reviews the design of mechanical components for process vessels in oil and gas facilities. The emphasis is on codes and standards sizing calculations and materials selection vessel specifi ...
A heat exchanger is a device in which energy is transferred from one fluid to another across a solid surface. Heat Exchangers (HEs) are used extensively and regularly in process and allied industries ...
This training course is a comprehensive course to the technology of shell and tube heat exchangers as these robust type of heat exchangers are the most commonly used in the process and refinery indust ...
Heat exchangers are designed to transfer heat more efficiently from one medium to another. Typically, heat exchangers use fluids to store heat but recently, with the creation of more advanced technolo ...
A heat exchanger is a component that allows the transfer of heat from one fluid (liquid or gas) to another fluid. Reasons for heat transfer include the following: • To heat a cooler fluid by means of ...
A heat exchanger is a component that allows the transfer of heat from one fluid (liquid or gas) to another fluid. Reasons for heat transfer include the following: • To heat a cooler fluid by means of ...
Introduce a team of fresh Mechanical Graduates, with different backgrounds, to various static equipments used in oil & Gas industry; particularly an overview of Block, PFD and P&ID presentation of equ ...
Providing services with a high quality that are satisfying the requirements
Appling the specifications and legalizations to ensure the quality of service.
Best utilization of resources for continually improving the business activities.
BTS keen to selects highly technical instructors based on professional field experience
Since BTS was established, it considered a training partner for world class oil & gas institution
1st floor, Incubator Buildingو Masdar City, Abu Dhabi, UAE
Sun to Fri 09:00 AM to 06:00 PM
Contact Us anytime!
Request Info