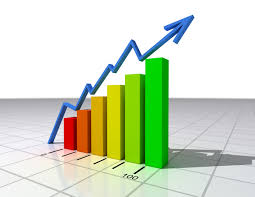
Highlights include:
By the end of this course delegates will be able to:
Quality Managers, Quality Assurance Engineers/Officials, Quality Engineers, Quality Improvement Professionals, Manufacturing/Process Engineers Project Managers, Corporate Managers, Executive Managers, Senior Managers, Middle Managers, Junior Managers, Human Resource Managers, Board of Directors, Entrepreneurs, Production Managers, Production Supervisors, Product Engineers, Inspectors, Line Leaders, Production Operators, Customer Service Professionals, Training Managers, Practitioners in the field of Quality Management, all those who are engaged in quality management implementation and improvement of organizational performance, those with an interest in quality management systems, those starting their career in quality management, staff who are involved in influencing, formulating or supporting the long term planning and strategy of the quality department or organization, as well as those who are responsible for linking, measuring and improving the performance of others
This interactive Training will be highly interactive, with opportunities to advance your opinions and ideas and will include;
Strategic Context
Effective Strategy Execution
Lean Awareness
Supplier Basics
Effective Leadership
Organisational Culture
Effective Teamwork
The Toyota Production System – A Philosophy Built on Lean
Creative Problem Solving
Tools Covered Include
Statistical Process Control
BTS attendance certificate will be issued to all attendees completing minimum of 75% of the total course duration.
Code | Date | Venue | Fees | Register |
---|---|---|---|---|
QUA101-01 | 13-04-2025 | Dammam | USD 5450 | |
QUA101-02 | 15-06-2025 | Jeddah | USD 5450 | |
QUA101-03 | 12-10-2025 | Dubai | USD 5450 | |
QUA101-04 | 14-12-2025 | Dubai | USD 5450 |
Many organizations have adopted structured approached to managing their operations through various different standards and techniques in order to manage quality assurance. This course will develop del ...
Quality Management has evolved to become an internationally sought and rewarding career. The quality management body of knowledge is developed to cover areas of leadership, communication, strategy, an ...
This interactive course is designed to develop the delegates’ skills in quality assurance and control and give them the best practices they require to implement different types of quality programs, in ...
Providing services with a high quality that are satisfying the requirements
Appling the specifications and legalizations to ensure the quality of service.
Best utilization of resources for continually improving the business activities.
BTS keen to selects highly technical instructors based on professional field experience
Since BTS was established, it considered a training partner for world class oil & gas institution
1st floor, Incubator Buildingو Masdar City, Abu Dhabi, UAE
Sun to Fri 09:00 AM to 06:00 PM
Contact Us anytime!
Request Info