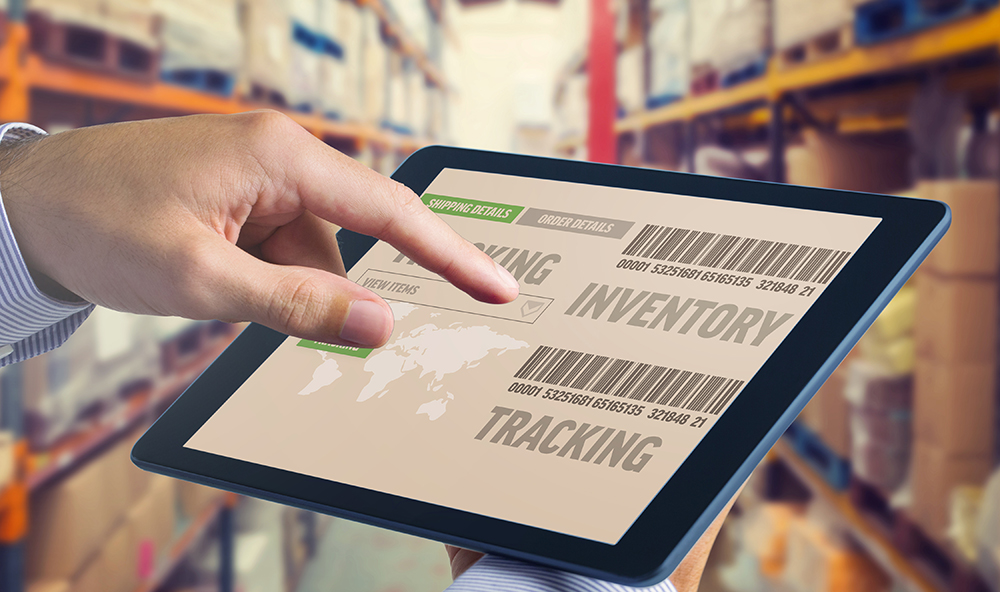
At the end of this conference the participants will be able to:
Unit 1: The Role of the Warehouse:
Unit 2: Product Classification:
Unit 3: Layout Options:
Unit 4: Methods and Equipment:
Unit 5: Health and Safety:
Unit 6: Security and Loss:
Unit 7: Productivity and Costs:
Unit 8: Service Levels:
Unit 9: Warehouse Layout:
Unit 10: Inventory and the Supply Chain:
Unit 11: Inventory Key Concepts:
Unit 12: Inventory Replenishment Methods and Systems:
Unit 13: Stock Control-Coding:
Unit 14: Stock Control-Recording:
Unit 15: Stock Control-Checking:
Unit 16: Inventory Performance:
Unit 17: Inventory Strategies:
Unit 18: Inventory Improvements:
BTS attendance certificate will be issued to all attendees completing minimum of 75% of the total course duration.
Code | Date | Venue | Fees | Register |
---|---|---|---|---|
LOG138-04 | 22-12-2024 | Dubai | USD 5450 |
Providing services with a high quality that are satisfying the requirements
Appling the specifications and legalizations to ensure the quality of service.
Best utilization of resources for continually improving the business activities.
BTS keen to selects highly technical instructors based on professional field experience
Since BTS was established, it considered a training partner for world class oil & gas institution
1st floor, Incubator Buildingو Masdar City, Abu Dhabi, UAE
Sun to Fri 09:00 AM to 06:00 PM
Contact Us anytime!
Request Info