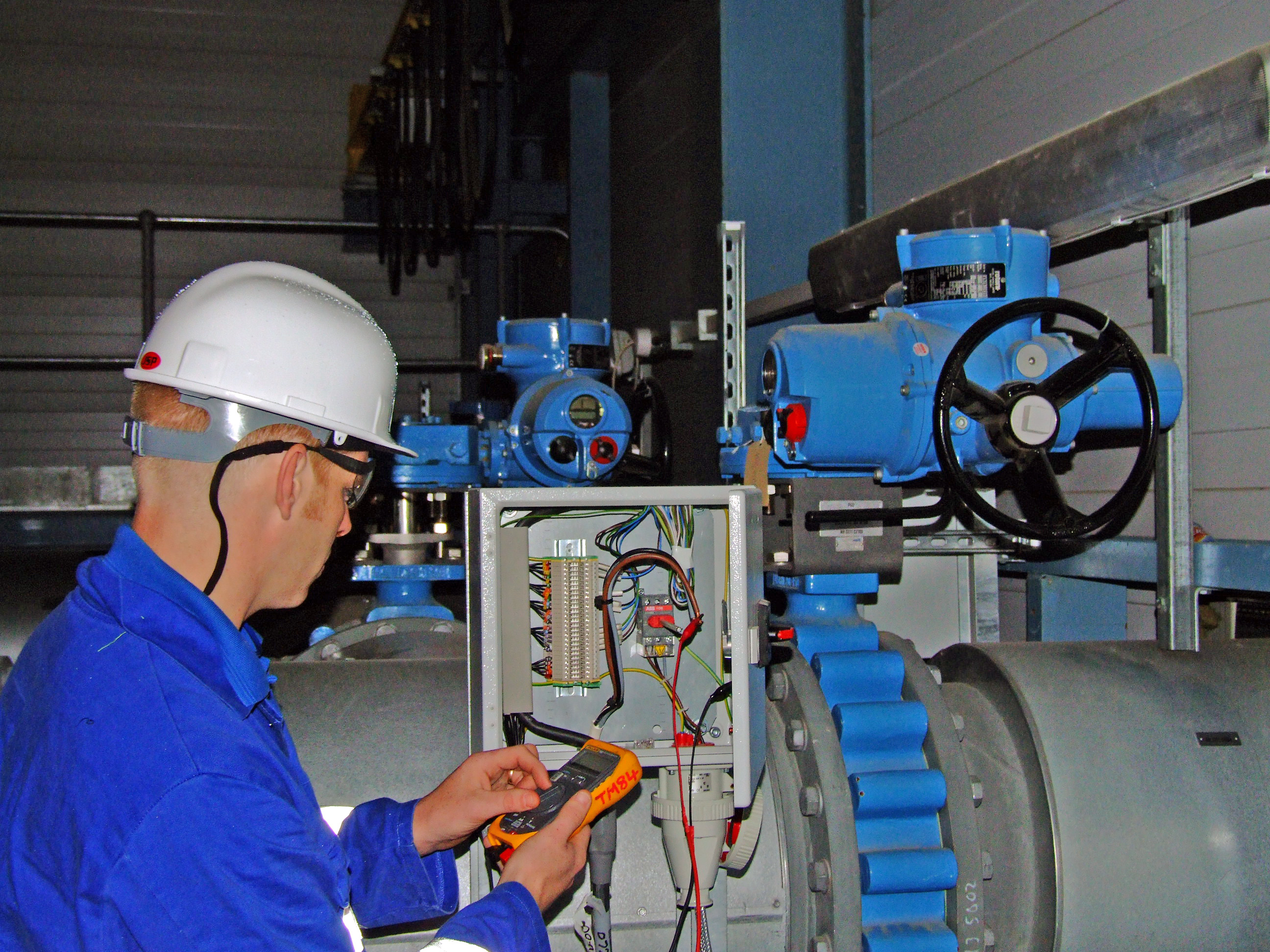
By the end of this training course, participants should be able to:
This training course would primarily be aimed at people within the Instrumentation, Electrical, Mechanical, Process disciplines, who are actively involved in the utilization of valves (control or shut-off) and actuators, as well as those people who have the additional responsibility of sizing the valves, and making a decision on the composition and make-up of the valve.
It would also be of great value to those individuals who either have a keen interest in the field, or who have to manage the people working on the various valves and actuators. (In this respect, one could think in terms of Process Control Engineers, Electrical Engineers, Mechanical Engineers, Industrial Engineers, Designers and the like.).
Day One
Practical – Understanding how valves operate, linear vs rotary, and single-action
Practical – Why is it important to achieve stability, when making use of a control valve? Can this stability be demonstrated?
Practical – Calculate a pressure drop that can be experienced
Practical – Converting from mA to percentage
Practical – Converting from percentage to mA
Practical – Working with voltage signals, that range from negative to positive
Practical – Dealing with, and understanding resolution, as can be expected, when sending a signal to a control valve
Practical – Reynolds number calculations
Practical – Do an assortment of pressure conversions, either using tables, or else provided software
Practical – Dealing with cavitation and flashing in a real-world scenario
Practical – Labelling of a control valve, from a diagram
Practical – Demonstrate how a valve can be utilised in an application, where there is combined feed forward and feedback control
Practical – Understanding the pressure drops that can be experienced, in pipelines that will contain control valves
Practical – Determining how long a tank will take to empty, should you need to fully open a control valve
Day Two
Practical – Choose the best valve to use, from a table, given specific criteria
Practical – Choose the best valve to use, from a flow chart-type diagram, given specific criteria
Practical – Convert signals from current, to their respective pressure equivalents
Practical – Interpret a P&ID diagram, than contains a control valve
Practical – Design a P&ID diagram, for a loop containing a control valve, using specific criteria that has been provided
Practical – Perform the amount of leakage that can be expected, based on criteria that has been provided
Practical – Understanding the equal percentage characteristics of a control valve
Practical – Understanding the linear characteristics of a control valve
Practical – Choosing the right characteristic, for various control scenarios and strategies that can be encountered
Practical – Visually see how the inherent characteristics can be altered, into installed characteristics, when a valve is installed in the field
Practical – Do all of the calculations, to come up with a control valve, that can be used in a specific application
Day Three
Practical – Making use of computer software, to size a control valve for a liquid application
Practical – Making use of computer software, to size a control valve for a gas application
Practical – How anti-reset windup can be a useful tool, with control valve applications. Delegates will work through a simulator, explaining this out in meticulous detail
Practical – Understanding what a valve positioner does, and how it will affect the operation of a control valve
Practical – Dealing with the issue of noise (as presented in a signal to the control valve), as well as the effects of a sticky valve, and how to counteract this
Practical – Making use of a table, choose the best material to use on a control valve
Practical – Making use of a table, evaluate the various corrosive effects that you may encounter, whilst using control vales
Practical – Making use of a table, evaluate whether your valve is going to be subject to noise / other damage, as a result of cavitation
Practical – Understanding the AUTO / MANUAL aspects of a controller, which will operate on a loop that has a control valve
Practical – The size of a control valve can cause significant changes to the Gain of the Process. This exercise calculates the Gain of a Process, for a specific control valve
Practical – Understanding the effects of Dead Time, on a control valve, and determining what this Dead Time is
Day Four
Practical – Choose the appropriate action that will be required, given a number of scenarios that the delegates will encounter
Practical – Experimenting with the P settings of a controller, understanding what the advantages and disadvantages are, and becoming fully comfortable with how changes will influence the operation of the control valve
Practical – Experimenting with the I settings of a controller, understanding what the advantages and disadvantages are, and becoming fully comfortable with how changes will influence the operation of the control valve
Practical – Experiment with a process, which has both adjustable P and I settings, and how this will affect the operation of a control valve
Practical – Experimenting with the D settings of a controller, understanding what the advantages and disadvantages are, and becoming fully comfortable with how changes will influence the operation of the control valve
Practical – Using the Ziegler-Nichols open-loop tuning methodology
Practical – Using the Ziegler-Nichols closed-loop tuning methodology
Practical – Making use of a Trial and error methodology, in the closed loop strategy
Practical – Making use of a Trial and error methodology, in the open loop strategy
Day Five
Practical – Experimenting with a control valve, that has been placed inside a cascade loop
Practical – Experimenting with a control valve, that has been placed inside a ratio-control loop
Practical – Coming up with a practical, useable solution, when excessive dead time is present in a loop that contains a control valve
Practical – Making use of a PLC simulator, get a control valve to work, using ON / OFF strategies
Practical – Demonstrate the PID blocks, used on a PLC, to control a control valve out in the field
BTS attendance certificate will be issued to all attendees completing minimum of 80% of the total course duration.
Code | Date | Venue | Fees | Register |
---|---|---|---|---|
IE110-01 | 12-01-2025 | Dubai | USD 5450 | |
IE110-02 | 11-05-2025 | Manama | USD 5450 | |
IE110-03 | 11-08-2025 | London | USD 6950 | |
IE110-04 | 19-10-2025 | Dubai | USD 5450 |
In most of oil and gas industries, petrochemical refineries, chemical, food industries the control valve play the most important part in controlling fluid flow and safety of process.
Extensive course materials provided contained useful information about valves/sizing and selection both theoretical and practical. You will gain a practical understanding of control valves, actuators, ...
Providing services with a high quality that are satisfying the requirements
Appling the specifications and legalizations to ensure the quality of service.
Best utilization of resources for continually improving the business activities.
BTS keen to selects highly technical instructors based on professional field experience
Since BTS was established, it considered a training partner for world class oil & gas institution
1st floor, Incubator Buildingو Masdar City, Abu Dhabi, UAE
Sun to Fri 09:00 AM to 06:00 PM
Contact Us anytime!
Request Info