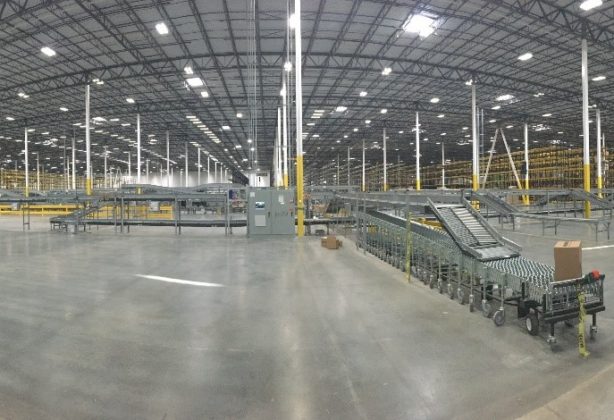
This course focuses on engineering materials and maintenance spares inventory, while providing broader coverage of the issues faced in managing this inventory. This course will be useful to anyone in industry who needs or wants to optimize spare parts inventory and increase cash flow.
By the end of this course delegates will be able to:
Warehouse and Financial Specialists, Account and Contract Specialists, Warehouse Engineers, Supply Chain Managers and Professionals, Logistic Administrators, Logistics Planning and Inventory Managers, Purchasing and Procurement Managers and professionals, Maintenance engineers, Projects and Planning Engineers, Electrical Engineers, Mechanical Engineers, oil & gas industry personnel.
This interactive Training will be highly interactive, with opportunities to advance your opinions and ideas and will include;
Linking Maintenance and Materials Management
Purchasing Parts
Layout and Security
Information Systems
Inventory Controls
Managing Repairable
Capital Projects
Service Improvement
Managing Personnel
Outsourcing Stores
Benchmarking Performance
BTS attendance certificate will be issued to all attendees completing minimum of 75% of the total course duration.
Code | Date | Venue | Fees | Register |
---|---|---|---|---|
LOG125-04 | 17-11-2024 | Dubai | USD 5450 |
Warehouses and Inventory Management are critical for the effective management of procurement and the supply chain to enable the efficient delivery of superior customer service. Warehouses and Inventor ...
In today’s competitive environment, the best supply chain will win. The chain that offers the highest value to its customers at the most efficient cost will have the competitive advantage. This requir ...
Providing services with a high quality that are satisfying the requirements
Appling the specifications and legalizations to ensure the quality of service.
Best utilization of resources for continually improving the business activities.
BTS keen to selects highly technical instructors based on professional field experience
Since BTS was established, it considered a training partner for world class oil & gas institution
1st floor, Incubator Buildingو Masdar City, Abu Dhabi, UAE
Sun to Fri 09:00 AM to 06:00 PM
Contact Us anytime!
Request Info