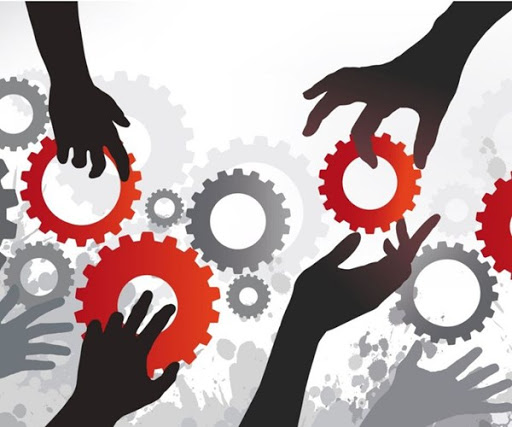
By the end of this course delegates will be able to:
Quality Managers, Quality Assurance Engineers/Officials, Quality Engineers, Quality Improvement Professionals, Manufacturing/Process Engineers Project Managers, Corporate Managers, Executive Managers, Senior Managers, Middle Managers, Junior Managers, Human Resource Managers, Board of Directors, Entrepreneurs, Production Managers, Production Supervisors, Product Engineers, Inspectors, Line Leaders, Production Operators, Customer Service Professionals, Training Managers, Practitioners in the field of Quality Management, all those who are engaged in quality management implementation and improvement of organizational performance, those with an interest in quality management systems, those starting their career in quality management, staff who are involved in influencing, formulating or supporting the long term planning and strategy of the quality department or organization, as well as those who are responsible for linking, measuring and improving the performance of others, all those who are responsible for, or indirectly involved in, a cost or profit center or a quality improvement function.
This interactive Training will be highly interactive, with opportunities to advance your opinions and ideas and will include;
Productivity Defined
Principles of Cost Reduction: The Quality Approach
Productivity Improvement Tools
Cost Reduction Opportunities
Measuring Your Productivity Initiatives
BTS attendance certificate will be issued to all attendees completing minimum of 75% of the total course duration.
Code | Date | Venue | Fees | Register |
---|---|---|---|---|
QUA114-01 | 11-05-2025 | Dubai | USD 5450 | |
QUA114-02 | 13-07-2025 | Manama | USD 5450 | |
QUA114-03 | 14-09-2025 | Dubai | USD 5450 | |
QUA114-04 | 16-11-2025 | Muscat | USD 5450 |
This course presents a blend between strategy and quality to help candidates develop the right skills to plan their organization's quality strategic plans. The course will take candidates through the ...
Total Quality Management (TQM) is a system of principles, methods, and best practices that provide a framework for organizations to strive for excellence in everything they do. Today business, governm ...
Total Quality Management (TQM) is an organizational management method that seeks to improve quality of products and services by implementing a process of continuous improvement. It is an approach to i ...
Quality management has evolved to become an internationally sought and rewarding career. The quality management body of knowledge is developed to cover areas of leadership, communication, strategy, an ...
Providing services with a high quality that are satisfying the requirements
Appling the specifications and legalizations to ensure the quality of service.
Best utilization of resources for continually improving the business activities.
BTS keen to selects highly technical instructors based on professional field experience
Since BTS was established, it considered a training partner for world class oil & gas institution
1st floor, Incubator Buildingو Masdar City, Abu Dhabi, UAE
Sun to Fri 09:00 AM to 06:00 PM
Contact Us anytime!
Request Info